Microsoft enables manufacturers to drive through the new era of productivity and transform themselves through the power of digital technology, empowering their staff and reshaping their industries.Using Microsoft technologies, manufacturers can deliver innovative products that customers want, faster. Connected product innovation solutions from Microsoft will help our customers design, develop, and improve products using technology to collaborate and create content based on information, analytics, and insights from customer interactions, product performance, and social networks, with real-time availability to accelerate innovation. Microsoft offers devices and apps that support design and engineering needs. The technologies enable teams to collaborate and communicate across geographic and organizational boundaries and extract insight from disparate data sources.
Modern Productivity
|
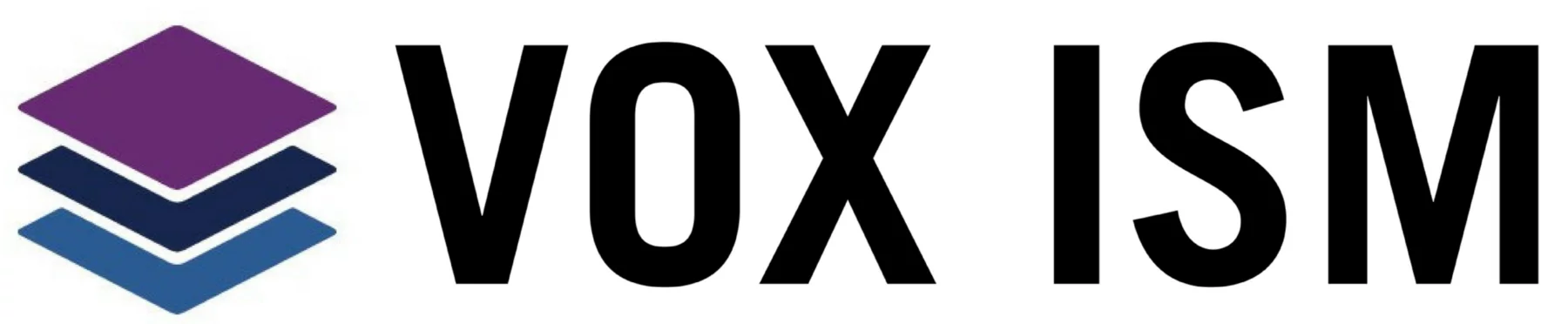