![]() |
Manufacturing & ResourcesDiscrete Manufacturing Article |
|
Article: The internet of things: creating connected operations in manufacturing
By Sanjay Ravi from OnWindows
Sanjay Ravi explains how Microsoft can help manufacturers take advantage of the internet of things to transform their business and enhance the customer experience in a quick and inexpensive way by leveraging their current technology landscape. There is a significant transformation happening in the manufacturing industry today. Business models are changing: manufacturers are moving from an asset-centric transaction to a service-centric relationship model; instead of selling only a manufactured product, they are also looking to selling a business service that goes along with the product. Internet of things is a key enabler that is driving this change, a network of smart and connected devices or sensors, which can collect and share data and provide significant new insight. In a B2C environment, by focusing on providing a connected device or experience, manufacturers can transform how they engage with consumers. Automotive manufacturers, for example, can communicate with customers when they are in their vehicle through a two-way in-car platform to provide value-added services, using vehicle related, location-specific, and consumer-context information. Or by equipping a tyre with a sensor, instead of selling the product, manufacturers can sell the miles their customers drive on it. Another example is the smart TV where manufacturers can also sell services through the product and provide a rich connected experience. Enrique Andaluz, industry solution manager, discrete manufacturing at Microsoft, explains: “Connecting operations help manufacturers leverage the opportunity to understand how their customers use the manufactured products and how the products perform. The revolution is that such visibility makes manufacturers innovate faster and more accurately on the way people use their products. It also helps them innovate around how and what services drive true value to their customers and the customer’s customer. Manufacturers need to embrace these revolutionary technologies quick if they want to maintain or gain leading edge.” On the B2B side, by modernising the architecture of manufacturing systems and interconnecting devices and people, manufacturers can quickly and cheaply increase the flow of information and enhance the interaction across trading partners. This allows them to monitor devices from remote locations to proactively offer new services such as condition-based maintenance that enhance equipment performance, or improve equipment uptime to lower operational cost. Manufacturers have better visibility and control to make sure the uptime of the equipment is very high, which can reduce costs and enhance equipment performance. It enables them to offer new services, because instead of just selling a product, they can sell an SLA for uptime and take responsibility for maintenance and repair. Take the example of an equipment manufacturer in Germany whose products are being used in a plant in South Africa. Today, if a problem arises in the equipment in South Africa, the plant is reliant on local technicians who can be expensive and may not be trained in this particular piece of equipment or have the skills to track down the issue. The manufacturer may have to send someone from Germany to South Africa to fix the problem. By putting sensors in the equipment, the German manufacturer can remotely diagnose the problem and address it there and then send very specific instructions to the local team on how to solve the problem. This results in better service that costs less and identifies and resolves problems faster, resulting in enhanced customer service experience. Andaluz explains the benefits for manufacturers: “When you think about connected operations by leveraging the internet of things, we need to consider the role of the internet of people and the internet of services as well. In this context, the value delivered comes from four different top pillars: people, process, asset and information. “Connecting people allows efficiency and productivity gains; connecting equipment allows for energy consumption and performance/maintenance management to avoid unexpected shut down – in general, it reduces operational cost by better managing assets; connecting parts allows for inventory and supply chain cost reduction; and connecting to end products allows improved quality and material flow as well as reduce logistic inefficiencies. Then by connecting both, parts and end products, you distil value from better managing the process they go through during manufacturing and distribution. And by connecting to the ecosystems, you can improve the economy of scale and address new market needs with innovative products and services; this comes as the result of exchanging data and useful information across people in the entire ecosystem.” The good news is that enabling this environment does not require a rip-and-replace approach. Manufacturers can leverage existing investments while adding on additional capabilities through analysis, the cloud and new devices. Microsoft’s breadth of capabilities and technology solutions presents a strategic and economic choice that is fast to implement and allows manufacturers to innovate and differentiate over the long term.
OnWindows.com is a third party publication providing news and industry thought leadership on Microsoft and partner technology in the enterprise. Microsoft has rights to reuse this article in MS-owned and third party publications and digital destinations. To do so, please state the author (at the top of the document) and OnWindows when republishing.
The OnWindows site and quarterly publication provide a wealth of information about how Microsoft and its partners are helping businesses in the financial services, communications and media, manufacturing and resources, retail consumer products and services, and public sectors. |
||
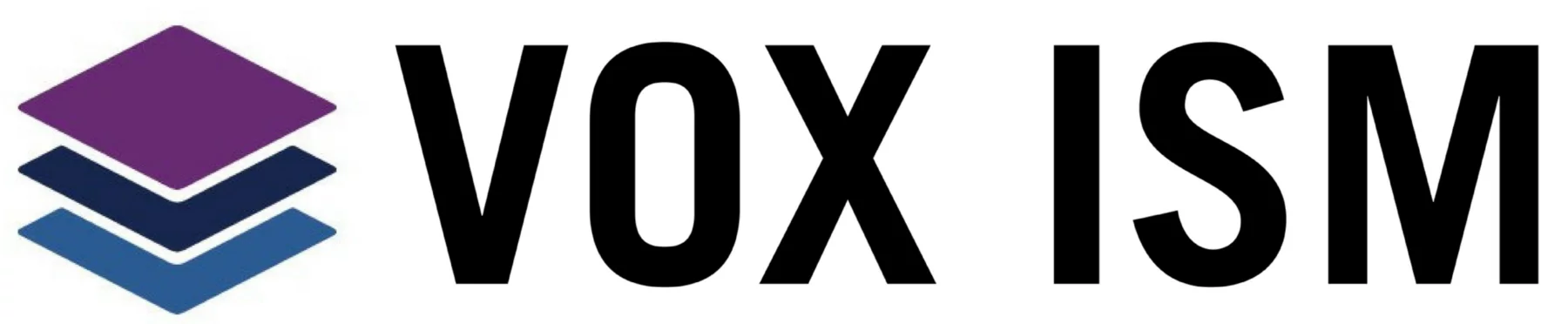