Forecasting is an essential part of planning. Without forecasting your inventory requirement, planning is not possible. And if you plan well you can achieve maximum order fulfilment with guaranteed customer satisfaction.
There are two significant forecast types that you can do to run a successful business-
- Sales/marketing forecast
- Operational forecast (includes production forecast, financial forecast and inventory forecast).
The operational forecast is mostly based on sales/marketing forecast; otherwise, also known as a demand forecast.
In manufacturing and distribution business, forecasting plays an essential role in identifying the cost of operations. One of the major contributor to operating cost is inventory cost. As per industry standard, the average inventory cost is 20-30% of total operating cost. If you want to reduce the operating cost/expenses, you need to focus on the inventory forecasting and replenishment.
Standard inventory planning in Microsoft Dynamics 365 Business Central is based on the investigation of the demand and supply situation of the item and calculation of the projected available balance. This necessary balance is defined in the picture below
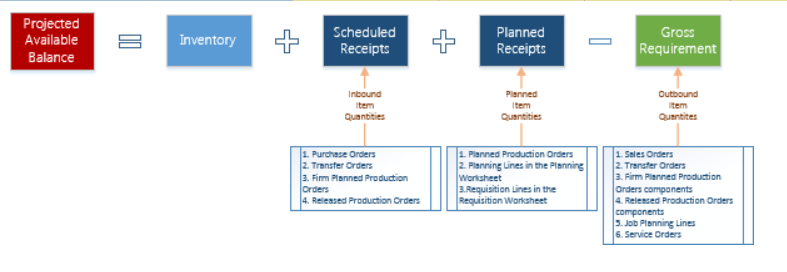
In Dynamics 365 Business Central, Inventory is a type of supply, but for inventory planning, the planning system distinguishes between two inventory levels:
- Projected inventory– is the quantity of gross inventory, including supply and demand in the past, even if not posted, when starting the planning process. The projected inventory is used by the planning system to monitor the reorder point and to determine the reorder quantity when using the Maximum Qty. Reordering policy.
- Projected available inventory – is the part of the projected inventory that at a given point in time is available to fulfil demand. The projected available inventory is used by the planning engine when monitoring the safety stock level. The projected available inventory is used by the planning system to monitor the safety stock level since the safety stock must always be available to serve unexpected demand.
If you notice, keywords while defining inventory are- reorder point, reorder quantity, reordering policy, safety stock, safety lead time, lead time, and planned receipts etc. These keywords are known as planning parameter in Business central. These are the parameters that the user sets for an item or a group of items control which actions the planning system will suggest in the various situations. The planning parameters are defined on each item card to control when, how much, and how to replenish.
One of the best parts of planning in Business Central is that it gives warning messages- Emergency, Exception and Attention; when you run planning worksheets. Along with these warning messages it suggests replenishment method; whether to change current purchase order quantity, create a new purchase order, club purchase orders. It gives a real-time inventory replenishment insights. You can review and do all the changes in one click. Or you can go to the item card, see the forecast and create PO’s directly.
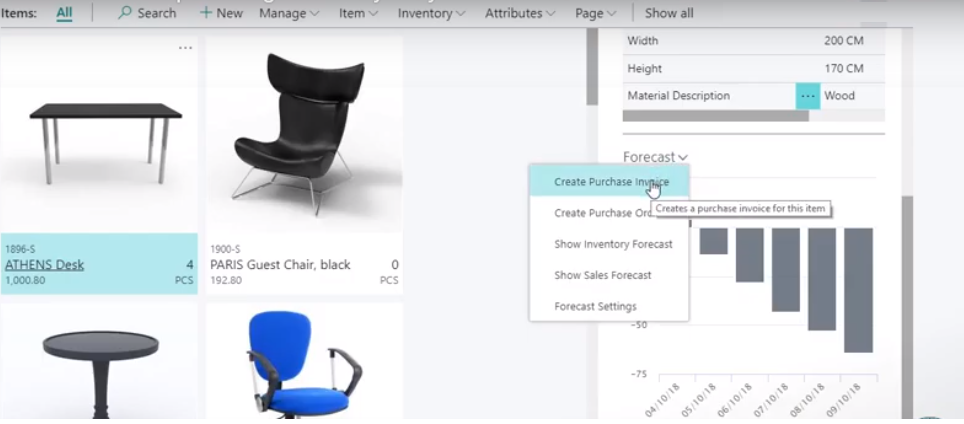
Key to optimum inventory is setting the parameters right, follow the insights, react to warnings.
Interested to know more?
Join us on June 12 for an exclusive webinar on “Forecasting inventory requirements in Business Central”.
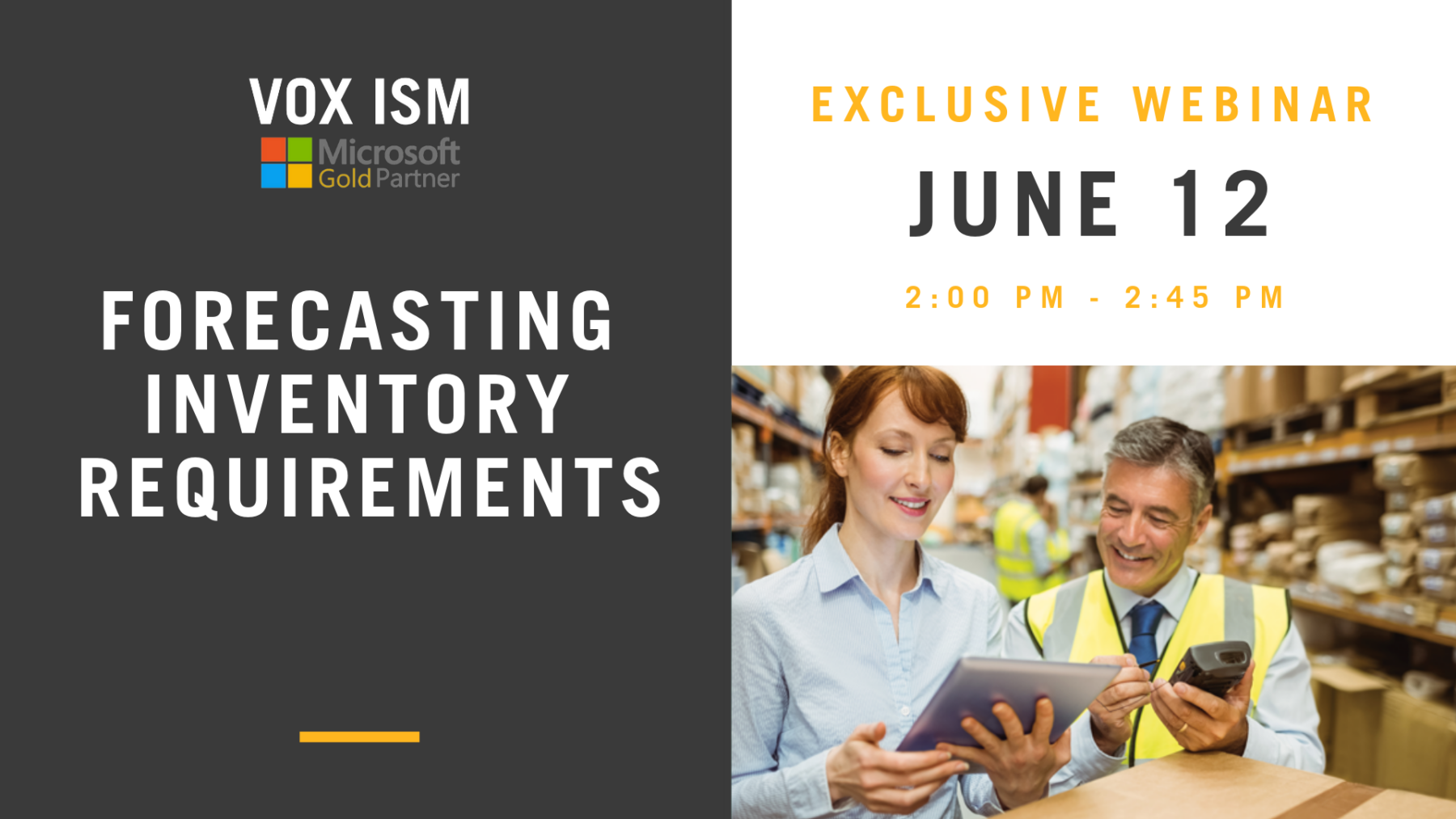