So you have discovered the limitations of using reorder point (ROP) inventory management and are wondering how, or having trouble with, the use of MPS/MRP? Join us as we delve into this more sophisticated method of managing demand and supply to keep inventory low and service levels high. We will be touching on the different types of plan calculation methods and how and when to use them.
Customers are transforming with Dynamics 365 Business Central
The terms “running the planning worksheet” or “running MRP” refer to the calculation of the master production schedule and material requirements based on actual and forecasted demand. The planning system can calculate either Master Planning Schedule (MPS) or Material Requirements Planning (MRP) on request, or it can calculate both at the same time.
- MPS is the calculation of a master production schedule based on actual demand and the demand forecast. The MPS calculation is used for end items that have a forecast or a sales order line. These items are called MPS items and are identified dynamically when the calculation starts.
- MRP is the calculation of material requirements based on actual demand for components and the demand forecast on the component level. MRP is calculated only for items that are not MPS items. The purpose of MRP is to provide time-phased formal plans, by item, to supply the appropriate item, at the appropriate time, in the appropriate location, in the appropriate quantity.
With each planned method, Microsoft Dynamics 365 – Business Central generates worksheet entries assuming infinite capacity. Work centre and machine centre capacity is not considered when you develop schedules.
Interested to know more?
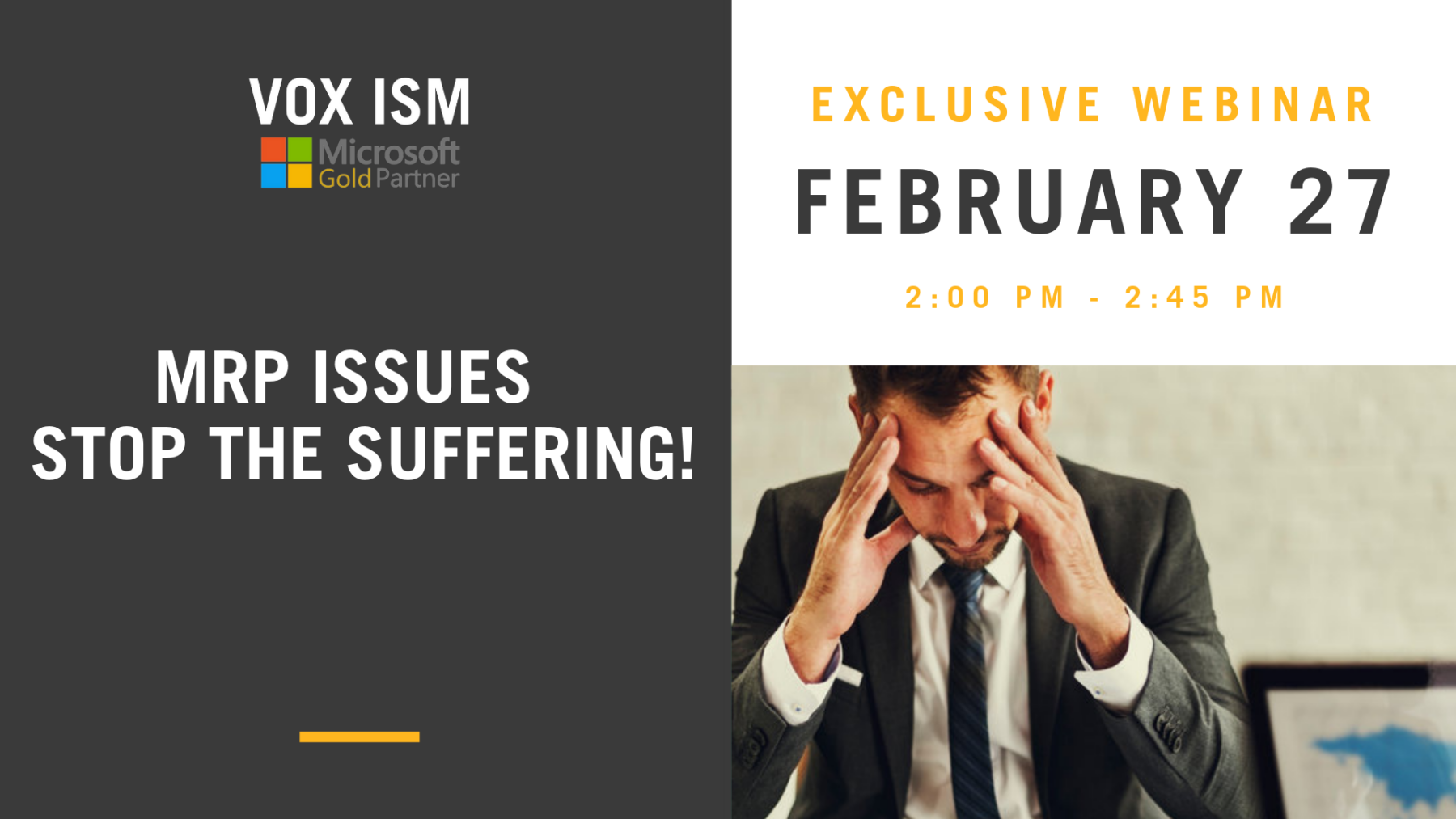
Joins us on February 27 for an exclusive webinar to get some insights in managing your inventory with Microsoft Business Central. Click here to register.
Blog post by Bob Dzimbowski – Manufacturing Consultant
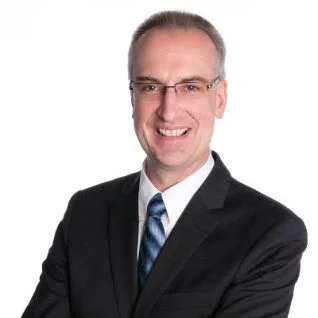
Bob is a Certified Supply Chain Professional and Certified in Production and Inventory Control, graduated with a BCom from York University. Specializing in inventory control, planning, purchasing, warehousing, and distribution, Bob has spent the last 37 years in Toronto in a number of industries including durable goods, construction, automotive, food and Pharma.