Every business wants to achieve goals with minimum effort. To achieve maximum efficiency, manufacturers and distributors need the right ERP tools to monitor and manage the shop floor to enhance & optimize business processes. Advanced Manufacturing uses new technologies to improve production efficiency to keep up the competitive market. We have many technologies in the market, such as cloud ERP that offer scalability, flexibility, and low capital requirements to access innovation. This reduces business costs to increase profits with timely delivery of quality products.
What is needed in an advanced manufacturing ERP system??
● Material Requirements Planning (MRP)
● Subcontractor management
● Advanced Planning & Scheduling (APS)
● Production Management
● Automated data collection
● Capacity Requirements Planning (CRP)
In this blog, we will discuss the first topic: Material Requirements Planning (MRP)
MRP is designed to answer three questions: What is needed? How much is needed? When is it needed? MRP works backward from a production plan for finished goods, which is converted into a list of requirements for the subassemblies, parts, and raw materials needed to produce the final product within the established schedule.
Material Requirements Planning in Business Central
Steps to Define parameters and Run MRP in Business Central
ITEM CARD:
In the Item card, to run MRP, we have to define a few parameters. In this blog, I have taken an example of a Finished item(HVAC equipment). When a sales order is created for the item and running an MRP system, it will suggest we make a production order for this HVAC equipment.
A replenishment system is the type of Supply order created when the items need to be replenished. In this Blog, it will be Production Order because Item is replenished by creating a production order for the FG.
Lead time specifies the amount of time it takes to replenish the order from the order created (10 Days for this HVAC).
Reorder point and reorder quantity are the reorder parameters defined. In this example, reorder point 10 defines that when the inventory is below the 10 units system, it will suggest reordering Units based on the reorder quantity defined(In this example, it is 20 Units).
Other parameters like Safety lead time, safety stock quantity, MOQ and maximum order qty can also be used to plan the replenishment.
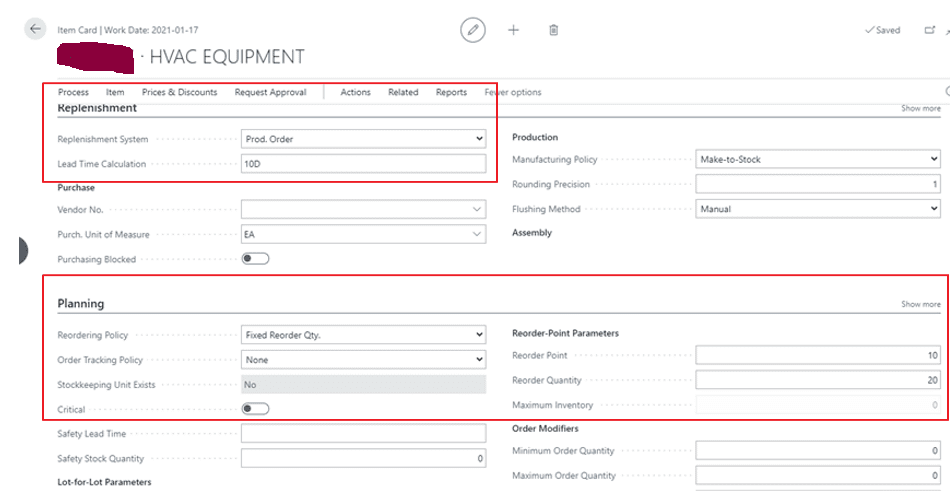
BOM Structure:
BOM Structure contains the information of the components used to produce the HVAC Equipment.
And a Replenishment system provides the details of how each component goes into the HVAC and is replenished. In this case, it is mostly by purchasing an RM from vendors.
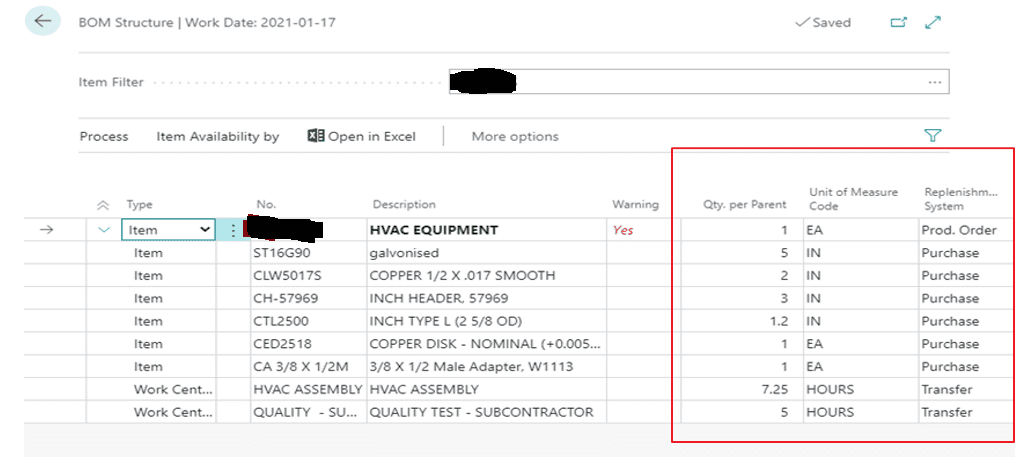
Planning Worksheet:
This Worksheet helps us understand what we need to produce/purchase based on the sales demand or forecast.
- Search for planning worksheets. Click on Calculate regenerate plan.
- Make use of the parameters like Start date and end date to define the demand for the period of time. It can take advantage of a few other filters like item number, Location code, Item category codes(groups) to plan only the required items.
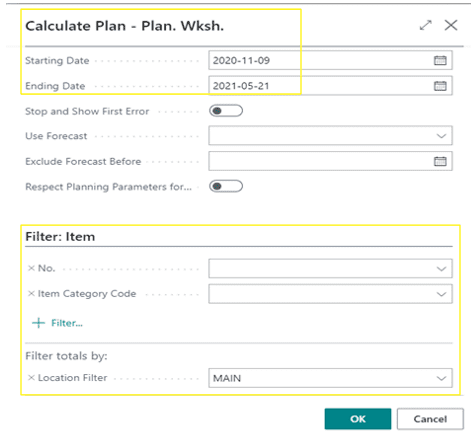
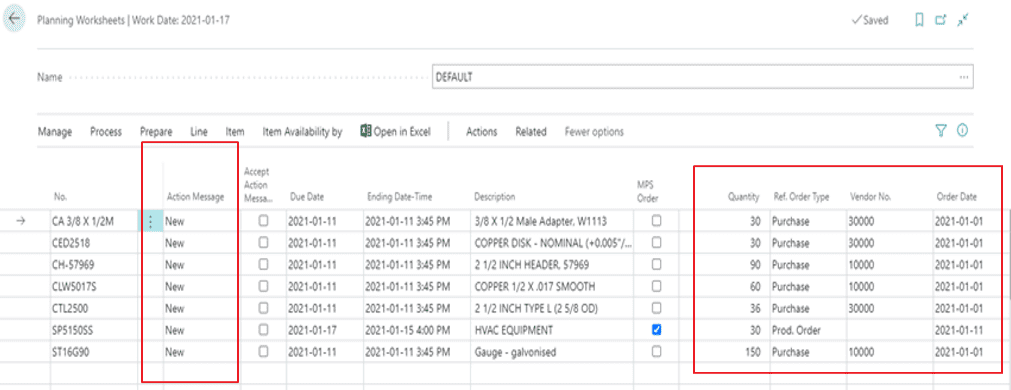
- The line with Ref. order type prod. Order is our production order. And purchase defines the demand for purchasing the product to finish the production orders issued. Whereas quantity defines the required qty to be purchased or produced with in the time defined.
- Vendor No. specifies the vendor who will ship the items in Purchase orders. An order date defines the date on which the order is required to be placed. This is calculated based on the lead time defined in the item card.
- Click on the field Carry out action Message and a below page will open.
- The worksheet lines checked the accepted and Replenishment system as Prod. Order, Purchase, transfer are converted to Firm Planned Production order, Purchase order and Transfer order respectively
Please note: All worksheet lines checked for Accept action messages are converted.
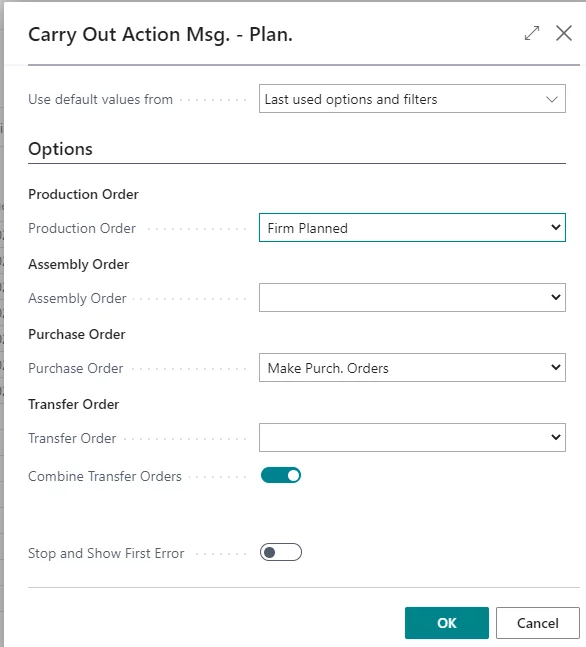
Conclusion:
Material Requirements Planning gives a manufacturing company to calculate the purchase and production requirement to fulfil the sales demand for the time period defined.
Join Rakshith K L from VOX ISM to learn more about running Material Requirements Planning in Microsoft Dynamics 365 Business Central ERP tool.
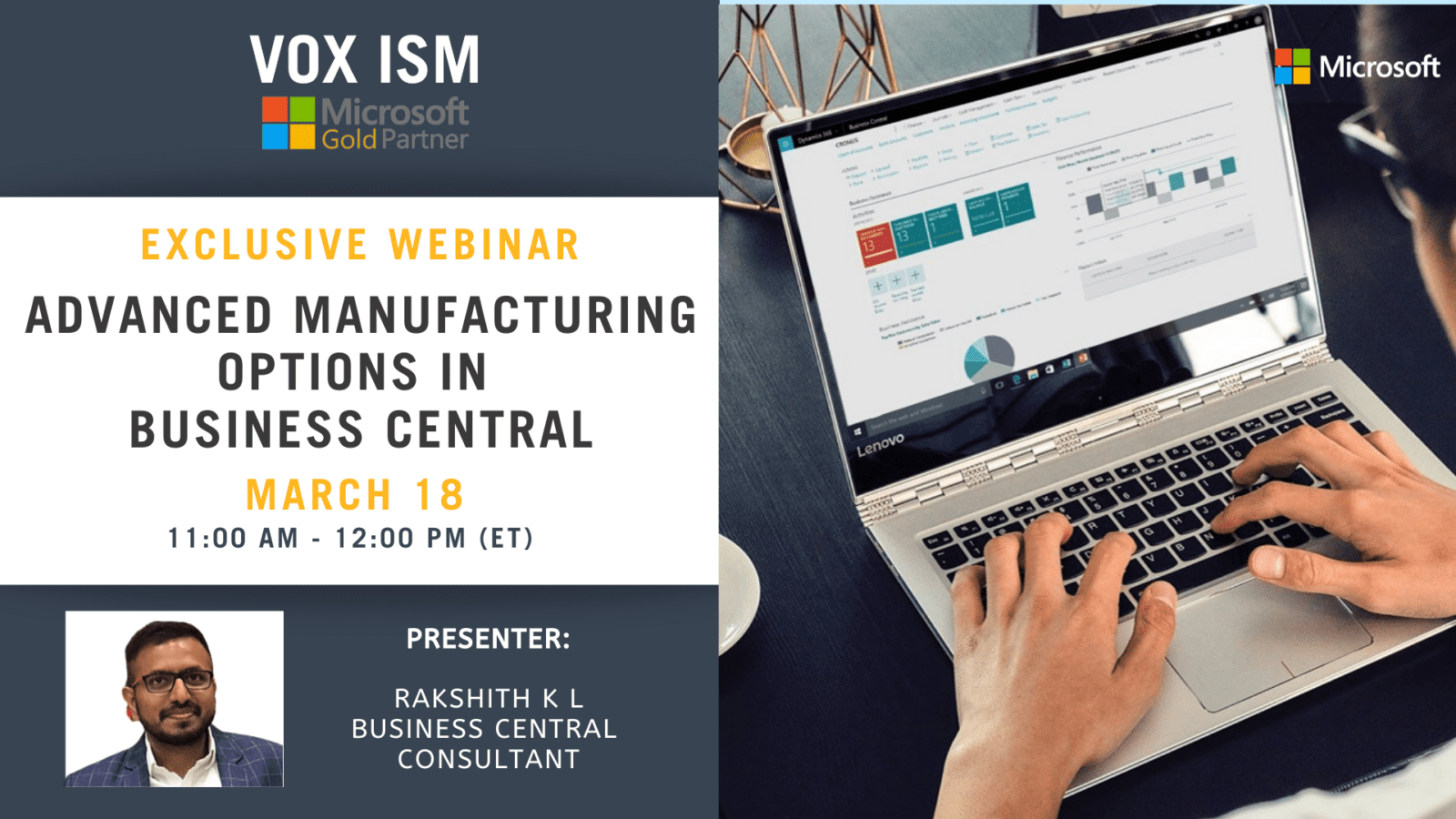