At VOX ISM, we service many manufacturers who are engineer-to-order (ETO). ETO means the company will design, build, install and service products specific to a customer’s need. Typically, the product is unique, one of a kind and has a very custom and complex BOM. This allows ETO companies to differentiate themselves in the market but also creates challenges.
CTO or configure to order represents a manufacturer that sells a baseline product, but that product can be modified with pre-engineered options.
The challenge in the ETO industry is that customers are expecting a quick turnaround of quotes and orders with high quality, and the process of engaging sales, engineering, production and customer service, all working in harmony, is essential and challenging.
Speed, effort, efficiency, accuracy and customer experiences are pitfalls or challenges that need to be overcome in these complex environments.
Software alone is not the answer and not giving the customer exactly what he wants is not a solution. But you can change the approach and philosophy of design and use software to assist
EXPLORING THE ISSUE
When customers ask for quotes, the typical approach is to create 3D models in your CAD software to determine the BOM. Once you have a BOM, you can accurately and efficiently calculate the total steel, components and hardware.
This is an example of complex BOM. Typically, an ETO company will not design entirely from scratch the product. They will have a library of pre-engineered the subassemblies and components that they can recycle or modify when building something new.
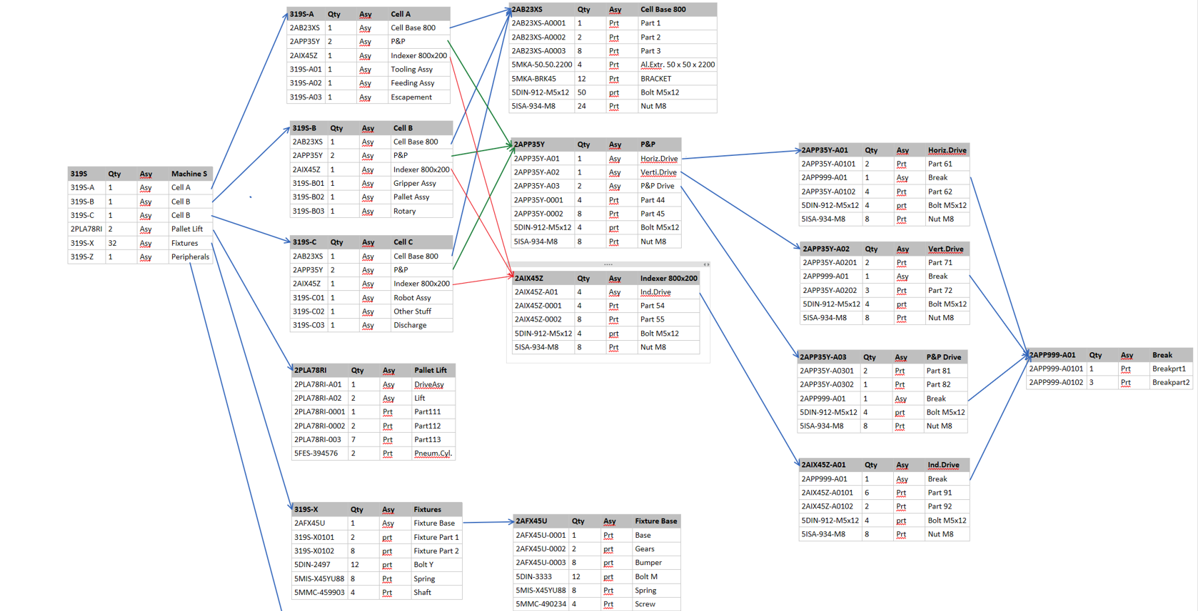
Instead of copying and building a brand new subassembly, the designer can strive to make the lower level assemblies more standard, universal and flexible.
MAKING SUBASSEMBLIES STANDARD
Think of it like pre-made Lego pieces. It becomes easier to create and build when forms are interchangeable. If you manufacturer the products you now have an opportunity to improve the quality through repeatability and potentially buy in volume and stock common products and reduce lead times.
In order to manage this in the ERP system, each subassembly must have it’s own BOM and revision level so that you can see where else the product is used.
Microsoft Dynamics has built-in version control and the ability to block BOM from being used while in design.
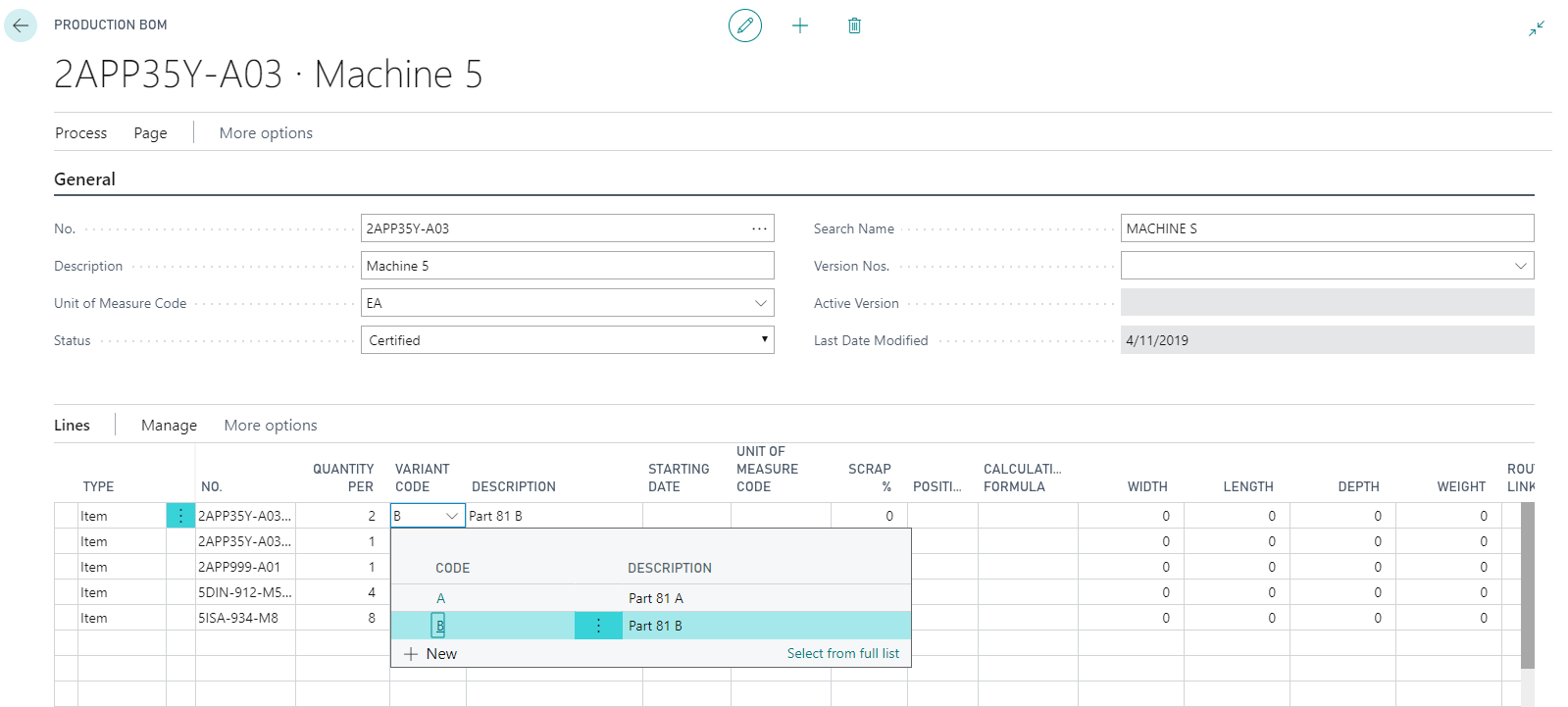
CONFIGURING A JOB
When creating your unique job you design and create the unique BOM at the higher levels or major pieces of equipment but at some point, you can start to reference the common or standard components. In this below example you can simply swap out the subassemblies you require (see in the job Cell A, B, C) and by refreshing the job it will pull in all other premade components.
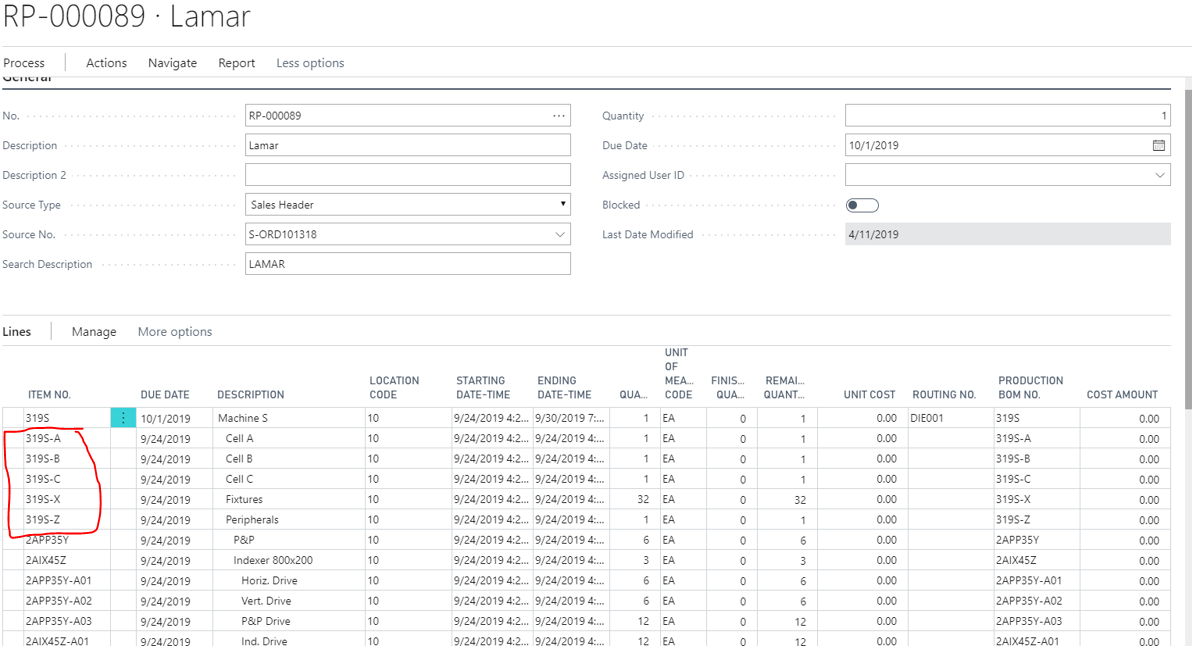
TIME AND ACCURACY
Because manually keying data into an ERP solution takes time and is error-prone, a bidirectional exchange of data between ERP and CRM and CAD systems not only eliminates the need to key data but more importantly, assures the data is identical in all systems.
At Vox ISM we recommend using CADLink to seamlessly create part numbers, update drawings, change revisions and create all of the subassemblies without errors at a click of the button into Microsoft Dynamics Business Central.
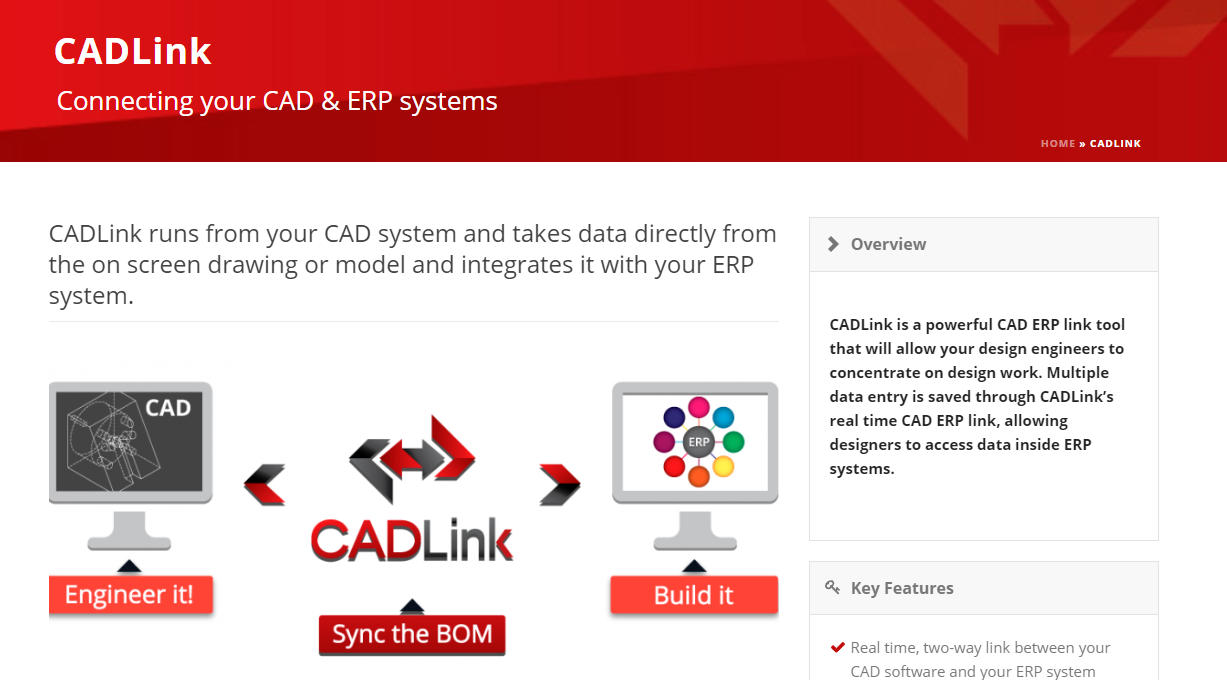
CADLink uses a real-time, bidirectional link to pull and push information from your CAD model and ERP system. Draw comparisons and make changes to two different data sets in one interface with CADLink to reduce making multiple data entries, and costly mistakes. CADLink can automatically create parts you just modelled in your item master, highlight discrepancies between the data sets and synchronize your CAD and ERP Bill of Materials in an organized and controlled way.
BENEFITS
Traditionally ETO companies rely on (one) senior engineer to estimate costs for quotes for sales. So if you can give salespeople a secure method (modular costing by components), they can quickly and easily generate quotes and estimates drawing on similar designs or previous production costs without worrying about each nut and bolt. When the job is awarded, the integrated BOM will flow seamlessly from design to purchasing and manufacturing, saving errors and time providing access correct information to eliminate questions, bottlenecks and delays.
In today’s world of customers wanting everything now and done right the first time, manufacturers need to update their systems and processes to eliminate constraints continually. Since ETO manufacturers don’t get a pass because their processes are more complex, they must continuously implement ways to offer increased value to their customers. Having an ERP system is one way to improve performance, but it is not enough. It needs to be combined with a design philosophy that not ‘everything’ is unique and ‘estimates’ are close enough. Integration to CAD makes it easy.
If you enjoyed this article, please see Qbuild at BMAC.
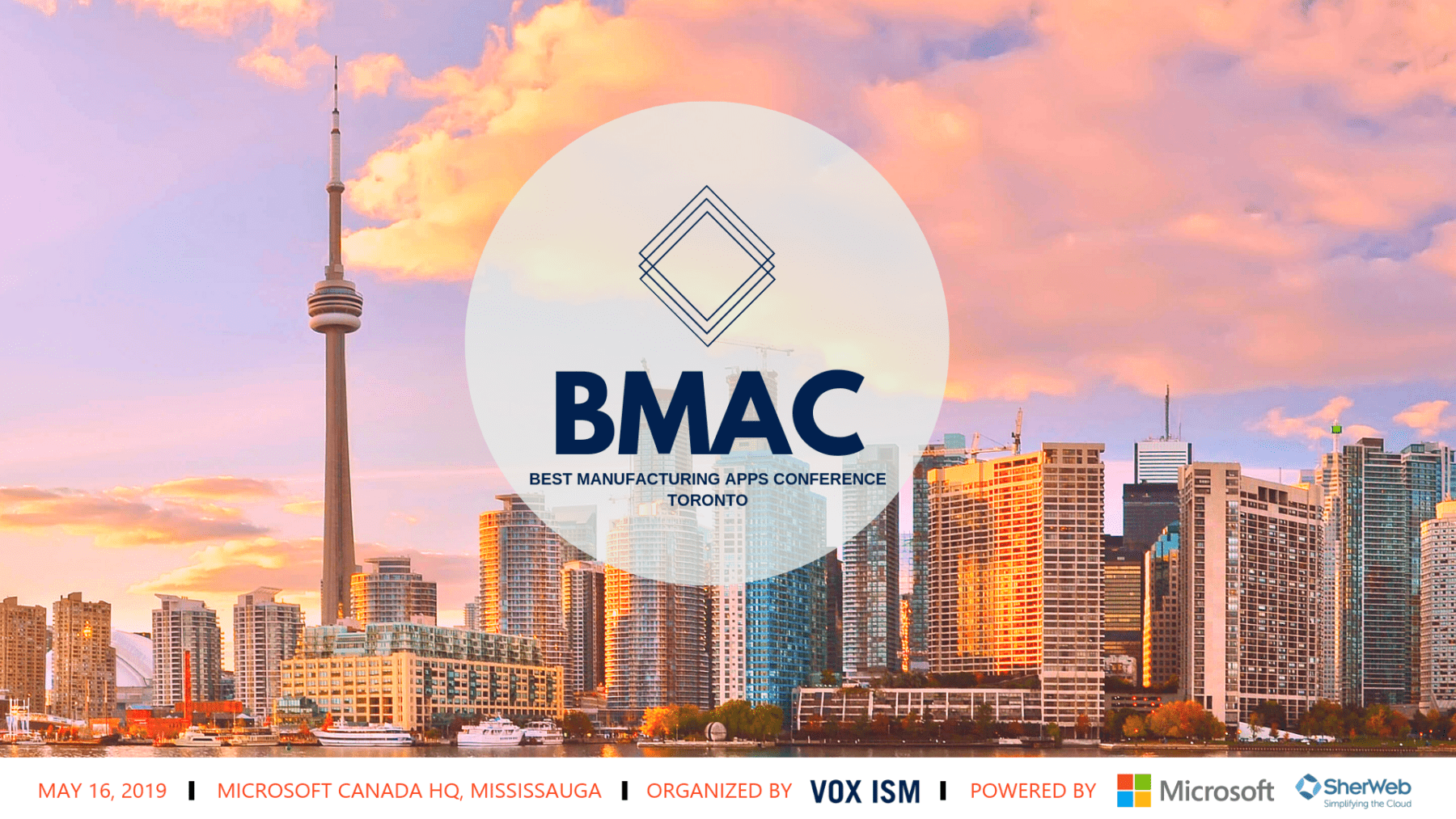
BMAC – Best Manufacturing Apps Conference. The BMAC is a one-stop experience that brings together Canadian manufacturers and industry experts and keeps them ahead of manufacturing’s digital transformation.
The Best Manufacturing Apps Conference 2019 will be held on May 16, at Microsoft Canada HQ, Mississauga from 1:30 PM – 3:00 PM.
Conference Agenda:
- Microsoft Dynamics 365 Business Central for Manufacturing– What Is New for Canadian Manufacturers in 2019
- 14 BMAC Exhibitors Will Present Their Product and Service in An Allocated Time Slot.
- An Open Exhibit Hall -Visit and Try Out the Software with The Exhibitor That Catches Your Attention.